About the Role
Job Description
Summary Statement:
This position is responsible for the operation and sanitation for the Processing Department. This position must monitor specific areas of the Conversion Department, assess process needs, and take appropriate steps to address the needs while focusing on safety, quality, cost, and delivery. The Processing Utility must demonstrate leadership ability, communication skills, ability to multi-task, and a strong working knowledge of plant production process policies. This employee must be flexible and able to work extended hours to provide plant coverage whenever necessary.
Primary Role and Responsibilities
- Understands the manufacturing processes and interactions between the different processing functions and recognizes optimization potentials
- Supports the Team Leader, Supervisor, and Business Unit Manager in all decisions
- Initiates corrective actions as appropriate and informs Team Leader/Supervisor of any deviation/variation from production plan, quality, safety, and cost goals
- Ensures the rules of safety, product quality, hygiene (GMP, HACCP, and ISO) are followed
- Ensures that all production data is entered and correctly followed up in relation to individual processing functions.
- Ensures the safety of all employees working in or around area
- Participates in start-up and hand-off meetings at the start and end of shift
- Ensures all processing equipment as well as facilities are properly cleaned and sanitized on a daily basis in accordance with Kraft Heinz Sanitation Procedures and Quality Expectation Standards
- Responsible for updating and maintaining calibrations for the FoodScan, ProcessScan, FT120, and all other NIR equipment
- Conducts and documents quality checks such as cook sheets, recording charts, temperature charts, and other process documentation
- Responsible for completing and documenting period work for the Processing Department
- Communicates with the Control Room Operator position regarding all aspects of the cream cheese process
- Ensures compliance to all plant rules and policies
- Support Plant Quality Systems
- Actively participates in the continuous improvement process
- Participates in CI work groups within the processing area as well as across the plant
- Reports any technical issues related to equipment and automation
- Continuously strives for improvements in regards to safety, quality, cost and delivery
- Includes other departments (maintenance, engineering, quality) for problem solving and improvements
- Perform all other duties as assigned
- Work according to safety requirements as identified in the Employee Handbook, plant safety programs, and job-specific detailed process sheets
- The ability to calculate and make decisions with respect to White Rinse capabilities, white rinse usage rates, white rinse quality, and salt and gum addition rates.
- Ability to communicate with all links of the white rinse process. (i.e. Separator Operators, Mix Operators, Sanitation Operators, Maintenance Department, etc.)
- Takes ownership of the management of salvage inventories, the white rinse and flavors flush systems.
- Washing and sanitizing equipment and equipment parts to ensure “safe” and excellent “quality” product (Lines, White Rinse Tanks, Flavors Flush Tanks, Whey Load Out Lines, Pumps, Air Valves, MSD Separator and intake silos)
- Perform all other duties as assigned by Supervisor or Team Leader
- Responsible to follow FSQ requirements such as GMP’s and other daily/job specific duties to support QRMP.
Additional Education/Certification/Skills:
English Language Skills – Able to speak, read, and write
Qualifications:
- Excellent knowledge and understanding of cream cheese technology and manufacturing processes
- Solid understanding of continuous improvement and lean manufacturing processes
- Good understanding of manufacturing cost aspects
- Must demonstrate the following leadership competencies
- Drive for Results
- Functional/Technical Expertise
- Communication Skills
- Problem Solving
- Taking Initiative
- Customer Service
- Required to perform job duties efficiently and safely
- Ability to lift up to 50 pounds and utilize plant approved safe lifting practices for over 50 pounds
- Ability to work extended hours and extended workweeks to cover the business needs
- Must have computer skills with knowledge of various software programs to include: Microsoft Word and Excel
- Must be a self-starter with the ability to work with minimal supervision
- Must be adaptable to change
- Must have demonstrated decision making skills
- Must adhere to all Kraft Heinz policies as stated in the Employee Handbook and follow internal Kraft procedures
- Minimum 2 years in manufacturing environment preferably in the cheese/dairy industry
- Internal candidates must have a demonstrated exceptional attendance history as well as a performance history
- Processing Utilities must attend and be current on Confined Space Training on an annual basis. Being Confined Space trained does not mean that you will be required to enter
Location(s)
Beaver Dam Plant
Kraft Heinz is an Equal Opportunity Employer that prohibits discrimination or harassment of any type. All qualified applicants are considered for employment without regard to race, color, national origin, age, sex, sexual orientation, gender, gender identity or expression, disability status, protected veteran status, or any other characteristic protected by law. Applicants who require an accommodation to participate in the job application or hiring process should contact NATAI@kraftheinz.com.
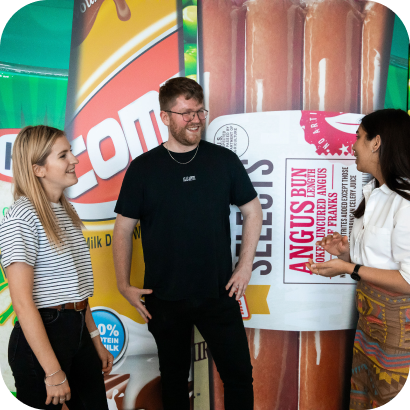
About Us
Kraft Heinz is a global food company with a delicious heritage. Our emerging and iconic food and beverage brands deliver the best taste, fun, and quality to every table we touch. Worldwide.
We’re on a mission to disrupt not only our own business, but the global food industry. Consumer obsession and unexpected partnerships fuel our progress. As we drive innovation company-wide.
Our people are connected by a culture of ownership, agility and endless curiosity. We believe in being good humans — working to improve our company, communities, and planet.
We’re proud of where we’ve been and even more thrilled about where we’re headed as we nourish the world and lead the future of food.