About the Role
Job Description
3rd Shift position-Tuesday-Saturday or Sunday-Friday (9:00pm-5:30am)
- $31-$39/hr
- Benefits (medical, dental, vison, 401k matching)
Purpose
Under supervision, maintains the daily operation of all facility equipment, which is related to the operation of ammonia refrigeration systems, facility utility systems to include air, water, gas, electrical, chemical, steam, and fire sprinkler. Responsible for installing, maintaining and repairing heating, ventilation and air conditioning systems. Other responsibilities to include performing routine building maintenance tasks and other scheduled assignments as required.
Principal accountabilities
Maintenance
Maintains and operates the Ammonia refrigeration system and associated equipment, boilers, hot water heaters, roof top HVAC units, air compressors, O-zone generation equipment, water softening equipment, Co-generation system, and fixed fire suppression systems in accordance with all established safety procedures, as well as Company Policy and state and federal regulations and codes. Under supervision, performs semi-specialized tasks in the maintenance of the general plant and/or office building in the skill areas of plumbing, carpentry, painting, cement applications, door repairs (personnel and industrial), maintains building lighting, rooftop ventilation units, fire sprinkler piping repairs, building electrical, and utilities Monitors, adjust, and maintains the waste water system and coordinates the repairs of wastewater system components including cleaning, troubleshooting, electrical and mechanical repairs. Understands, troubleshoots, and repairs of all previously stated equipment and systems. Conducts maintenance daily checks, logs and readings on previously stated equipment and systems. Performs preventive and corrective maintenance on previously stated equipment and systems as assigned to maximize uptime and operating efficiency. Identifies all parts, supplies, and services required to maintain assigned areas and shifts. Conducts routine inspections of walls, floors, ceilings, insulations, piping, roof, parking lot, waste water system, etc. Performs minor electrical maintenance to include but not be limited to replacement or repair of fixtures (e.g. wall switches and outlets, incandescent and fluorescent bulbs and tubes, ballast, sockets, fuses, minor appliances, cords, etc.) using appropriate hand, power and specialty tools. Replaces or updates inoperable or old building materials and appliances (e.g. motors, belts, pumps, window glass, sinks, doors, smoke alarms, cabinets, shelves, tile, light fixtures, filter systems, patios etc.) to provide a safe, comfortable working environment for employees using various tools and materials (e.g. welding equipment, ladders, power saws, hammers, drills, etc.).
Reporting
Updates Computerized Maintenance Management System (CMMS) in support of Preventive & Corrective Maintenance.
Safety
Ensures a safe and sanitary work environment at all times while following established safety regulations in the performance of all job tasks and reporting any unsafe conditions immediately. Adheres to the Process Safety Management (PSM) / Risk Management Program (RMP) and Hazardous Waste Management Programs related to the ammonia refrigeration system to insure compliance with city, state, and federal environmental regulations. Complies with environmental regulations, Good Manufacturing Practices (GMP) and the plant’s Maintenance Safety Programs.
Control Costs
Completes work orders in a timely manner meeting or exceeding pre-established deadlines to reduce downtime and meet production goals. Ensures all quality standards are met or exceeded. Recommends changes established manufacturing processes to reduce or eliminate down time, increase operational effectiveness, and improve routine maintenance in all assigned areas and shifts.
Internal Customer Service
Works with Production Department to determine optimal time for any needed repairs on equipment. Follows through to ensure repairs are made on schedule. Informs Production Supervisor and Maintenance Supervisor of any issues. Establishes positive working relationships with all plant personnel.
Qualifications
EPA Section 608 Universal Certification maintained Proficient in welding ( Stick, MIG, TIG, Soldering / Brazing) Certification of Qualification on the Delimex ammonia refrigeration system, CO2 system, PSM process and facility SOP’s Understanding of steam principles and facility steam systems with the ability to troubleshoot pumps, valves, piping and water treatment General knowledge of the plant air system, water system, and Fire Protection System
Quality
Interprets and takes ownership of GMPs and food safety company standards. Must be able to provide recall information for raw material usage as well as disposals. Coordinate with Quality Assurance on any product placed or released from hold status, raw materials as well as finished product. Participate in the QRMP yearly audit and assist in the development of procedures and corrective actions. Accountable for the QRMP (Quality Risk Management Process) system and operational standards as outlined in the plant accountability list in order to achieve targeted RCR.
Manufacturing Playbook
Participates in the implementation of the factory’s playbook , especially in the pillar assigned to the department, to ensure successful completion of all checklist items/actions within the playbook.
The preceding functions have been provided as representative of the types of work performed by the employees assigned to this job classification. Management reserves the right to add, modify change or rescind the work assignments of this and different positions and to make reasonable accommodations so that qualified employees can perform the essential functions of the job.
Knowledge / skill / experience levels
The Utilities and Building Fabric Technician must possess knowledge of and understand the following:
- Basic maintenance principals regarding refrigeration, HVAC, compressed air, water, steam, gas, oil, chemical, and fire protection systems.
- HAZMAT, PSM, RMP, OSHA regulations, plant Maintenance Safety Program, and GMPs affecting all aspects of PM/CM safety within the plant and facilities.
- Understanding of steam principles and facility steam systems with the ability to troubleshoot pumps, valves, piping and water treatment.
- Policies, procedures, methods, and processes for performing preventive maintenance in assigned area(s) of responsibility.
- Measures to improve production efficiency, equipment performance, product quality, and plant safety.
- Parts and supplies required to support assigned areas and shifts.
- Plant’s quality standards, policies and procedures.
The Utilities and Building Fabric Technician must possess the following skills:
- Operate the ammonia refrigeration in accordance with all established safety procedures, codes, and regulations.
- Diagnose malfunctions/hidden defects in equipment and machinery and repair of all assigned equipment previously mentioned.
- Read wiring diagrams, blue prints, schematics, and manuals and logs.
- Basic welding ( Stick, MIG, TIG, Soldering/Brazing).
- Enter data into CMMS.
- Update maintenance logs.
- Implement measures to improve routine maintenance, production efficiencies, operational effectiveness, equipment performance, and safety in all assigned areas and shifts.
The Utilities and Building Fabric Technician must possess the following minimal education and experience:
- High School Diploma.
- HVAC Certification through an accredited vocational school. EPA Section 608 Universal Certification maintained
- Understanding of steam principles and facility steam systems with the ability to troubleshoot pumps, valves, piping and water treatment.
- General knowledge of the air systems, water systems, and Fire Protection Systems.
Preferred
- Three (3) years of experience in the refrigeration Food Industry and ammonia refrigeration.
- Basic welding certification through accredited vocational school.
Within first 3 months on the job
- Certification of Qualification on the Heinz ammonia refrigeration system, CO2 system, PSM process and facility SOP’s.
Within first 6 months on the job
- Must be able to pass and maintain a medical fitness evaluation and requirements for using an APR respirator and SCBA
- Certification as an Ammonia Refrigeration Assistant Operator through RETA.
Within first 12 months on the job
- Hazmat Certified (40 hour HAZWOPPER Certification) maintained.
Organizational relationships
Immediate Supervisor (title): Environmental/ Facilities Supervisor
Subordinates (titles): none
Other Job Titles Reporting to the Same Immediate Supervisor: Ammonia Refrigeration Foreman, Ammonia Refrigeration Operator Ammonia Refrigeration Assistant Operator, Facilities Technician.
For updated job descriptions
ADDITIONAL INFORMATION/SUPERVISOR COMMENTS
The Utilities and Building Fabric Technician displays the following winning work attributes:
- Treats others with dignity and respect.
- Demonstrates flexibility and openness to change.
- Actively cooperates and encourages cooperation from others.
- Maintains a calm and controlled demeanor, especially in stressful situations.
- Responds resourcefully to change and ambiguity.
- Demonstrates commitment to self improvement.
- Complies with laws and the company’s ethical principles.
- Focuses time and energy on established priorities.
- Makes decisions under conditions of uncertainty.
- Takes action and reliably delivers on commitments.
- Allocates time efficiently to meet production goals.
- Effectively balances multiple demands and competing priorities.
- Builds quality into every dimension of work.
- Is accessible and supportive of others.
- Demonstrates awareness of customer needs.
- Strives to achieve quality standards in all work.
- Applies best practices as they learn them.
- Is on time at the beginning of work and adheres to breaks and lunch schedules.
- Is thoroughly prepared at the beginning of work.
- Is productive throughout the entire work day or shift.
- Strives to improve their job knowledge and job skills.
- Helps others, when help is needed.
- Is a positive team member who supports the company and its initiatives.
- Actively participates in meetings.
- Maintains a positive attitude and builds positive relationships throughout the plant.
- Establishes and maintains positive relationships with vendors and others providing service to the plant.
- Is accurate and attentive to detail.
- Requires minimal supervision.
- Able to multi-task as needed.
- Good communicator.
- Able to work varying shifts 1st, 2nd & 3rd.
Physical demands
Regularly required to bend and twist at the waist, stand for prolonged periods, walk frequently, crawl, climb, work at heights and on stairs and on ladders. May be required to lift up to 50 lbs without assistance. Vision requirements include close vision, distance vision, peripheral vision, depth perception and ability to adjust focus.
Work environment
The incumbent works with and near hazardous equipment/ machinery (mixers, hoppers, conveyor belts, ovens, fryers, etc.) in a large, open food processing plant. There is exposure to dust, gas, or fumes and food odor throughout a shift. Hearing protection is required throughout the production and packing areas. Lighting is fluorescent. Floors in the production, packing areas, and warehouse are concrete and sanitized. They may be wet. All employees wear protective gear. Temperatures vary throughout the plant and can be very hot if working near ovens and cold elsewhere.
We are an equal opportunity employer and value diversity at our company. We do not discriminate on the basis of race, religion, color, national origin, sex, gender, gender expression, sexual orientation, age, marital status, veteran status, or disability status. We will ensure that individuals with disabilities are provided reasonable
Location(s)
Delimex – Hourly
Kraft Heinz is an Equal Opportunity Employer that prohibits discrimination or harassment of any type. All qualified applicants are considered for employment without regard to race, color, national origin, age, sex, sexual orientation, gender, gender identity or expression, disability status, protected veteran status, or any other characteristic protected by law. Applicants who require an accommodation to participate in the job application or hiring process should contact NATAI@kraftheinz.com .
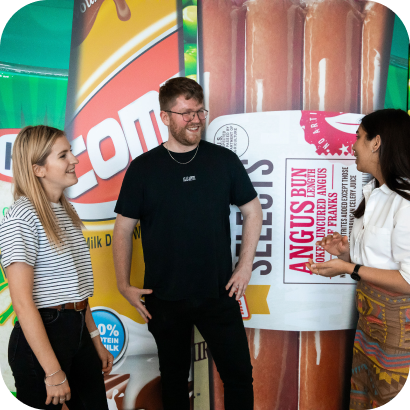
About Us
Kraft Heinz is a global food company with a delicious heritage. Our emerging and iconic food and beverage brands deliver the best taste, fun, and quality to every table we touch. Worldwide.
We’re on a mission to disrupt not only our own business, but the global food industry. Consumer obsession and unexpected partnerships fuel our progress. As we drive innovation company-wide.
Our people are connected by a culture of ownership, agility and endless curiosity. We believe in being good humans — working to improve our company, communities, and planet.
We’re proud of where we’ve been and even more thrilled about where we’re headed as we nourish the world and lead the future of food.